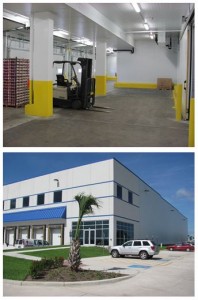
So what’s the big deal? The answer is in the acronym.
I – Insulated
That’s the “magic” if you will. IMPs are exceedingly efficient, lightweight and cost-effective insulators. With nominal R-values of R-8 per inch, there is virtually no equal. Further, since the insulation is encapsulated between two metal skins, there is little to no long-term loss of R-value over time. The insulation is a closed-cell foam comprised of billions of tiny bubbles acting like miniature double-paned windows. The bubbles contain dead air (gas) trapped inside. Since there is no better insulator than dead air, these tiny bubbles give the foam its tremendous thermal performance.
M – Metal
Durable, recyclable, formable, hard, strong, fire-resistant metal. Metal is a tremendously diverse material that the construction industry readily embraces. When used to make an IMP, metal protects the insulation and gives the panel its strength to resist the elements. The metal skins are fused to the foam core creating composite strength. This strength allows for fewer structural supports leading to installation efficiency and speed. Fewer girts equals decreased erection times. To protect against corrosion, the metal skins are typically G90 galvanized or coated in Galvalume.
P – Panels
IMPs are lightweight, modular building products that are easy to ship and quick to assemble.IMP manufacturers offer panels for exterior walls, interior walls, ceilings, soffits and roofs. With 42” being the standard width, installers are allowed to be super-efficient and cover a lot of ground in a hurry. Additionally, utilizing specialized vacuum-lift equipment makes handling and setting these panels a snap. Most IMPs come with an integral tongue-and-groove joint facilitating a quick, easy and, most importantly, weathertight installation. Since installers are ultimately responsible for a weathertight installation, most find that the single-component nature of IMPs lends itself to keeping the elements where they belong: on the outside of the building envelope.
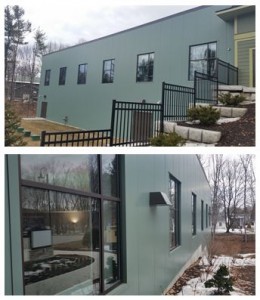
Now, should we think of IMPs primarily as metal cladding or rather should we think of them as just a “prettier,” more durable form of insulation? The answer is “yes.” We should view IMPs as both and classify them as one or the other depending on application. In their most rudimentary role, IMPs are simply a very durable insulation. The cold-storage industry is by far the largest purveyor of IMPs in this application. Nothing serves a cold-storage application better than an IMP. As stated previously, the R-values/inch are unmatched. The cold-storage industry can be generally defined as an industry that processes and stores anything perishable. This would include the processing of proteins like beef, pork and poultry, the storage of fruits and vegetables as well as seed storage, plus cheese making and beer brewing, just to name a few. It’s a sure bet that the food in your fridge spent time in a factory, distribution center and/or retail store wrapped in IMPs. Most of the products used in this industry would be termed standard: standard color (white), standard finish (embossed), standard width (42”), standard thicknesses (4, 5 and 6-inch), standard metal gauge (26) and finally, standard lead times (4-6 weeks).
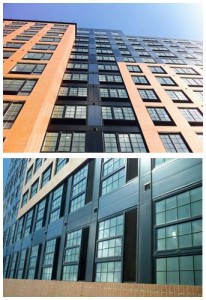
In the more recent past, due to more stringent energy codes and the public’s green movement, IMPs have enjoyed a steady push into the Commercial/ Industrial, Institutional and Architectural markets. In these markets, IMPs are more properly defined as pre-insulated cladding. There is a general consensus that using more and better insulation is not only the smart thing to do but also the responsible thing to do. Regardless of your stance on energy conservation and the green movement, a better insulated structure simply saves money. Therefore, institutions like schools, churches and hospitals have found IMPs to be a cost-effective and aesthetically pleasing way to put roofs and walls on their structures. Along with saving energy, IMPs can also be used to make beautiful architectural statements. The IMP manufacturers have gone above and beyond to offer the architectural community a diverse product line offering a myriad of different colors and visual effects. IMPs can be installed vertically or horizontally with different reveals and finishes. Factory formed corners are available as well as panel end-folds. All of these processes give the panels a sleek, high-end appeal readily embraced by the public.
Based on their inarguable diversity and recent gain in popularity it seems prudent to embrace IMPs exactly for what they are: a beautifully strong and thermally efficient metal cladding product. Not unlike the standing-seam roof before it, most believe IMPs will revolutionize certain sectors of the construction industry. They are readily available, easy to install and day after day designers seem to find new and exciting applications for this dynamic and versatile building product.